A warehouse can be fraught with safety hazards which, if left unchecked, can cause serious harm to your employees or
visitors. Warehouse checklists assist in identifying hazards and assessing risk in your workplace. It’s
imperative safety checks are carried out regularly to ensure you and your team maintain a safe working environment.
Consider these following elements as a good starting guide to developing a customised checklist for your warehouse.
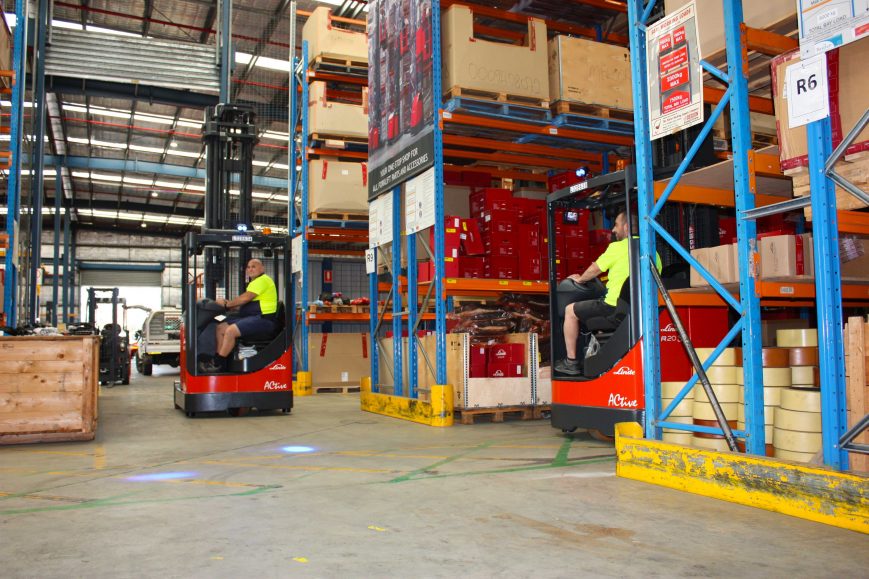
General safety
Some basics you should consider when developing a safety checklist:
- Are there any exposed/open loading docks or areas where employees could potentially fall from a height of one
metre or more? If so, install fall protection devices or structures.
- Are there any slip or fall hazards on your floors or in your aisles, for example clutter, rubbish, spills or
electrical cords? If yes, get rid of them.
- Are your employees, who have to do physical work, trained on safe work practices? If not, organise regular
compulsory training.
- Is your warehouse well ventilated? Be sure that it is, especially if you house chemicals.
- Is your machinery safe to use with your inventory, and fit for use in an indoor environment? If not, speak to
your machinery supplier to find the right type of equipment.
- Is your warehouse temperature monitored and controlled where applicable? You want to ensure you have optimal
temperatures so that:
- Your inventory is not impacted from the area being too cold or too hot
- Your staff are comfortable i.e. air conditioning/ heating
- Do your employees have all of the correct safety workwear to enable them to work safely and comfortably within
the warehouse? If not, ensure it is provided.
Material handling
It’s imperative your team are aware of how to safely handle the materials you house in your warehouse, not only
for operator safety but also for the safety of everyone working around them. Here are some tips to help you
formulate a materials handling checklist.
- Make sure there is a safe clearance for equipment and materials through the aisles and doorways
- All machinery should be checked daily, or prior to use, to ensure there are no failing mechanisms
- Vehicles need to be shut off with the brakes applied before loading and unloading
- It would be advantageous to have a blue spot light fitted to your unit as a safety precaution
operating in the warehouse (see picture)
- Ensure the correct securing chains, ropes, or slings are used for each specific job to be performed
- Covers and/or guardrails must be provided to protect your workers from stair openings in floors, equipment pits,
and other hazards
- Ensure every operator is aware of the WHS guidelines with regards to manual handling legislation
Electrical safety
Sometimes there can be complacency around electrical safety. Here are some tips to assist you in getting the basics
covered.
- Ensure there is correct training carried out for all employees where applicable, and that they possess the
correct competency and licensing to perform their tasks
- Employees must perform preliminary inspections and/or appropriate tests before beginning work on electrical
equipment or lines
- Portable electric equipment and tools must be either grounded or double insulated
- Any equipment with exposed wiring or cords with frayed or damaged insulation must be repaired or replaced
immediately
- Flexible cords and cables must be free of splices and/or taps
- Employees who regularly work around energised electrical equipment or lines should be trained in CPR
Whilst these guidelines will give you a good start in creating your own customised warehouse safety checklist, you
should also make it a point to consult all resources available to you. This means working with multiple partners
including:
- Referring to your state’s government run WHS leader for the latest in safety resources:
- Working with your equipment suppliers to ensure
- Adequate training is supplied on an ongoing basis
- Adequate safety solutions are in place on all pieces of
equipment and corresponding storage areas
- If you’re using fleet telematics software, that the data is analysed
correctly so well informed decisions can be made to ensure the safety of your crew
- Regular servicing is carried out so your equipment remains
safe to use and lasts as long as possible – if your supplier is unable to provide servicing then
make sure it’s performed by a licensed professional
- Consultation with relevant stakeholders including workers and employees
If you need assistance setting up your warehouse to run as safely as possible, contact us. We’ll
come out to your site, anywhere in Australia, to review your set up and work with you to provide a suitable material
handling solution for your purpose and budget.
At Linde Material Handling Australia we give you the Power to
Choose with a broad range of new, used or rentable material handling equipment. With our Value, Performance and Performance Plus
ranges, we can cater for any budget from businesses requiring just one truck all the way up to fully automated
robotic warehouses. Get in touch today!
Contact Us